The tire granulation line is engineered to produce high-quality crumb rubber (1~5mm) for diverse applications, while efficiently liberating 99.9% of steel wires and nylon fibers. This advanced system combines a tire shredder, rasper, granulator, magnetic separator, and nylon separator, all seamlessly integrated and controlled by a smart PLC system for optimal performance.
- Tire Type: Nylon tire, radial tire, OTR tire
- Output Size: 1~5 mm
- Capacity: 500~5,000 kg/h (or higher)
- Rubber Purity: 99.9%
- Usage: Rubber floor, rubber tile, artificial grass, pyrolysis oil
Working Process
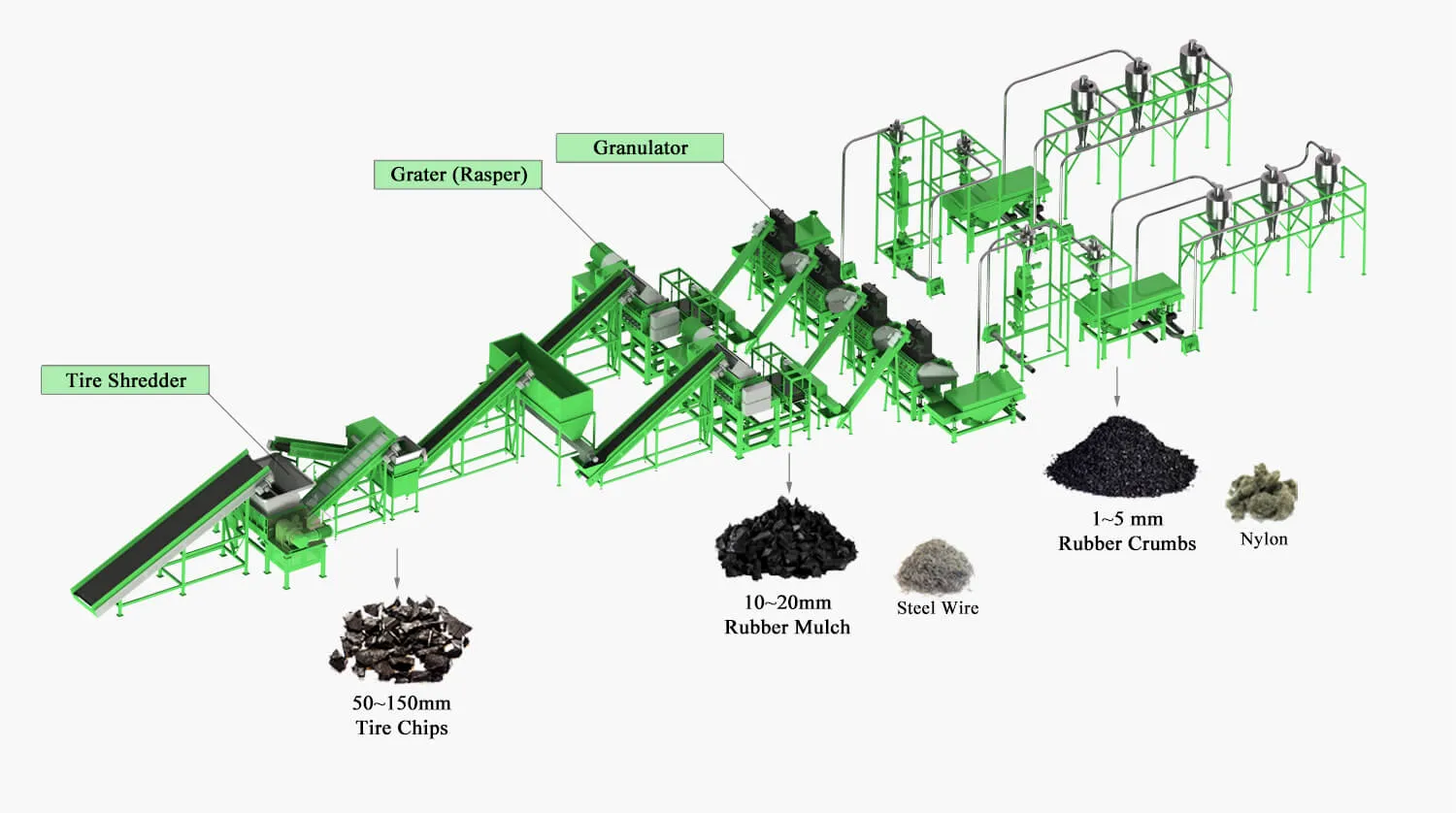
-
Step 1 (Optional): Use a tire debeader to extract thick steel wire rings from tire beads. Powered by a hydraulic cylinder, this machine efficiently removes bead wires. Customers can opt for a double-hook debeader to simultaneously extract wires from both sides of the tires, enhancing productivity.
-
Step 2 (Optional): A tire cutter can be used to slice large tires into shorter segments, making them suitable for smaller shredders. This step is unnecessary if a large-capacity shredder is already in place, saving time and resources.
-
Step 3 (50~150 mm): The tire shredder processes tires into uniform-sized chips. Optional equipment like a tire debeader or cutter can be added based on tire size and shredder model. EcoShred’s engineers will recommend customers the ideal screen system to ensure efficient operation.
-
Step 4 (10~30 mm): Transfer the tire chips via a belt conveyor to the rasper, where high-speed rotating shafts with grate blades tear and extract steel wires from the rubber mulch (10~30 mm). 99% steel wires will be removed by magnetic separator after the rasper.
-
Step 5 (1~5 mm): The rubber mulch is transported via a feeding conveyor to the granulator. Inside the cutting chamber, spinning knives dice the rubber into small cubic crumbs while breaking down nylon fibers, 80% nylon fiber will be separated by a primary nylon separation device after the granulator.
-
Step 6: A vibrating screen conveyor transfers the material to the nylon separator, equipped with an additional magnetic separator to remove any remaining nylon fibers and residual steel wires, delivering pure crumb rubber for final use.
Specification
Model | Capacity | Output Rubber Size | Purity | Total Power | Required Worker | Required Space | Power Consumption |
---|---|---|---|---|---|---|---|
ESG-500 | 500 kg/h | 1~5 mm | 99.90% | 257.9 kW | 2~3 people | 20*12*6 m | 180 kWh per hour |
ESG-1000 | 1000 kg/h | 1~5 mm | 99.90% | 290.9 kW | 2~3 people | 21.3*12*6 m | 204 kWh per hour |
ESG-2000 | 2000 kg/h | 1~5 mm | 99.90% | 486.6 kW | 2~3 people | 27*13*6 m | 340 kWh per hour |
ESG-4000 | 4000 kg/h | 1~5 mm | 99.90% | 887.1 kW | 2~3 people | 55*13.5*7m | 532 kWh per hour |
Note: we can customize any capacity based on customer’s requirement. |
Show Room
- High Automation: Reduces labor costs and simplifies the operation process.
- Improved Efficiency: Optimizes production speed until it reaches maximum performance.
- Precise Control: Ensures consistent product quality (size and purity).
- Reliable Operation: Low failure rate with built-in fault diagnosis.
- Flexibility: Adaptable to various tire types and production needs.
- Data Tracking: Records production data for analysis and optimization.
- Enhanced Safety: Automatic shutdown in case of abnormalities.
Applicatons
Have Any Question? Get In Touch Please !
If you have any question about tire recycling equipments, Please do not hesitate to contact us. We would reply to you as soon as possible.