ESP tire powder milling line is manufactured to transform waste tires into ultra-fine powder, ranging from 30 to 100 mesh. With this line, you can get super pure and top-quality black rubber powder for a wide range of demanding industries, such as rubber products, modified asphalt, reclaimed rubber, and even part of the ingredients for making new tires.
- Tire Type: Nylon tire, radial tire, OTR tire
- Output Size: 30~100 mesh
- Capacity: 500~5,000 kg/h (or higher)
- Rubber Purity: 99.9%
- Usage: Rubber tile, rubberized asphalt, reclaimed rubber
Working Process
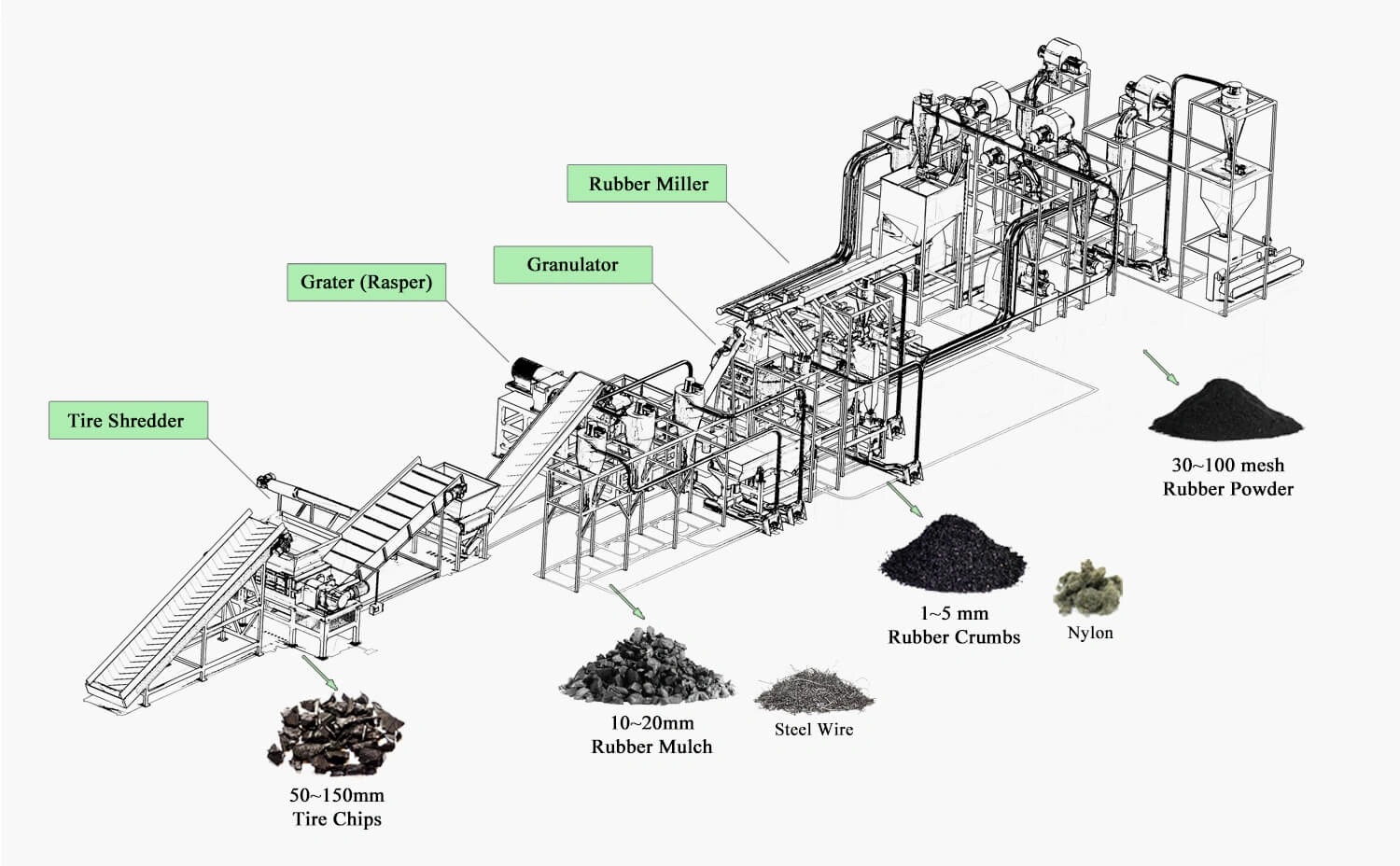
-
Step 1 (50~150 mm): The shredder is the first step in the process, where waste tires are cut into smaller chips. The material is fed into the shredder via a conveyor belt, and rotating blades break down the tires in pieces, and screen out the similar size tire chips that will be transported to the next stage.
-
Step 2 (10~30 mm): In second stage, the tire chips are chewed by the rasper teeth to further reduce in size, then the resulting mixture material will be transferred through a neodymium magnetic separator, where the steel wires will be picked out, then the rubber mulch will be conveyed to the granulator for finer processing.
-
Step 3 (1~5 mm): The granulator further processes the rubber crumbs into smaller granules using rotating blades. The granules are then sorted by size, with smaller granules passing through the screen and being sent to the nylon separator. A vibrating screen conveyor is equipped after the granulator to separate most of the nylon fibers from the rubber granules.
-
Step 4: The zig-zag nylon separator removes any remaining fiber or nylon from the rubber granules. Using air flow and vibration, the lightweight fibers are separated from the heavier rubber, which is then transported to the powder mills for final processing. And the nylon fiber will be collected from nylon outlet.
-
Step 5 (30~100 mesh): With the servo-motor powder mills, the rubber crumbs are ground into ultra fine powder, ranging from 30 to 100 mesh. The material is processed through high-speed grinding mills, and the final powder is collected for use in various industrial applications.
Specification
Model | Capacity | Output Rubber Size | Purity | Total Power | Required Worker | Required Space | Power Consumption |
---|---|---|---|---|---|---|---|
ESP-400 | 400 kg/h | 30~100 mesh | 99.90% | 450.8 kW | 2~3 people | 36*12*6 m | 315 kWh per hour |
ESP-800 | 800 kg/h | 30~100 mesh | 99.90% | 597.5 kW | 2~3 people | 39*13*6 m | 418 kWh per hour |
ESP-2000 | 2000 kg/h | 30~100 mesh | 99.90% | 1353.25 kW | 2~3 people | 48*14*6 m | 947 kWh per hour |
Note: we can customize any capacity based on customer’s requirement. |
Show Room
- High Automation: Fully automated control, requires minimum operators to operate the whole plant.
- High Tire Adaptation: Adaptable to all kinds of tires, including motor tires, car tires, truck tires, and OTR tires.
- Precise Control: PLC systems can adjust parameters accurately, ensuring uniform powder size and high quality.
- High Purity: Neodymium permanent magnet and zig-zag nylon separator guarantee a high removal rate of steel wires and nylon fibers.
- Flexibility: Can adjust to produce full-range sizes to meet different market needs.
- Data Recording and Analysis: Real-time production data tracking for process optimization and quality control.
- High Reliability: Low failure rates and super easy to maintain under automatic detection.
- Exceptional Precision: Servo motors provide precise speed and torque control, ensuring consistent and fine rubber powder quality.
Applicatons
Have Any Question? Get In Touch Please !
If you have any question about tire recycling equipments, Please do not hesitate to contact us. We would reply to you as soon as possible.